Electric Waterjetting Pumps for Offshore Hazardous Areas
To support offshore platform electrification we have further developed our high pressure, electrically driven waterjet unit for ATEX Zoned operation. We have combined proven reliability with state-of-the-art motor drive technology to provide the latest in electric waterjetting pumps for offshore hazardous areas.
- Electric-driven waterjet pumps for ATEX Zone 1 and Zone 2.
- Lower purchase price and running costs than diesel drive.
- Pump, motor and VSD all housed in one offshore container.
The MultEjet is developed as an alternative to diesel driven units. It utilises an integrated VSD to control the pump speed and yet retains the same footprint as diesel units. We continue to select the Hammelmann pump for its reliability and long service intervals and the MultEjet can be fitted with Hammelmann 70, 140 or 200 series pumps. These electric jetters use the very latest drive train technology and fewer parts giving improved reliability and reduced operating costs. The MultiEjet is part of our zero emissions future and the design has taken into account emerging technologies in order to future proof the units.
Pumping in ATEX and NORSOK Hazardous Areas
We designed the MultiEjet for operation in ATEX Zone 1 and Zone 2 operations. We also build to NORSOK specifications for operations on the Norwegian continental shelf. Find out more about our extensive experience of designing pump packages for hazardous environments.
What is different about our electric waterjetting pumps?
- features new drive train technology. This allows us to incorporate variable speed control without need for a separate VSD.
- features improved fine speed control.
- fits within the existing diesel unit footprint.
- is adaptable to meet various performance requirements.
- design is future proofed to suit emerging battery technology as it develops.
- can be designed to suit a wide range of supply voltages and frequencies.
- limits start-up current to suit available power supply.
- is more efficient than the fixed speed/diesel unit due to optimisation of total current to motor.
- speed can be automatically adjusted to maintain a set flow or pressure. For example, to extend nozzle life.
- has smooth starting, acceleration and deceleration.
- has an increased power factor resulting in greater efficiency. Reduced harmonic options are available.
- has a greater range of stopping options (controlled stop) increasing operator protection.
- has variable speed (50% – 100%) allowing greater
range of flow adjustment than a traditional diesel
engine unit. Further speed reduction options are
available.
Get in touch
To discuss your offshore jetting equipment requirements, give us a call: +44 1905 751790 or email sales@calder.co.uk
Alternatively, discover more about our fabric maintenance range.
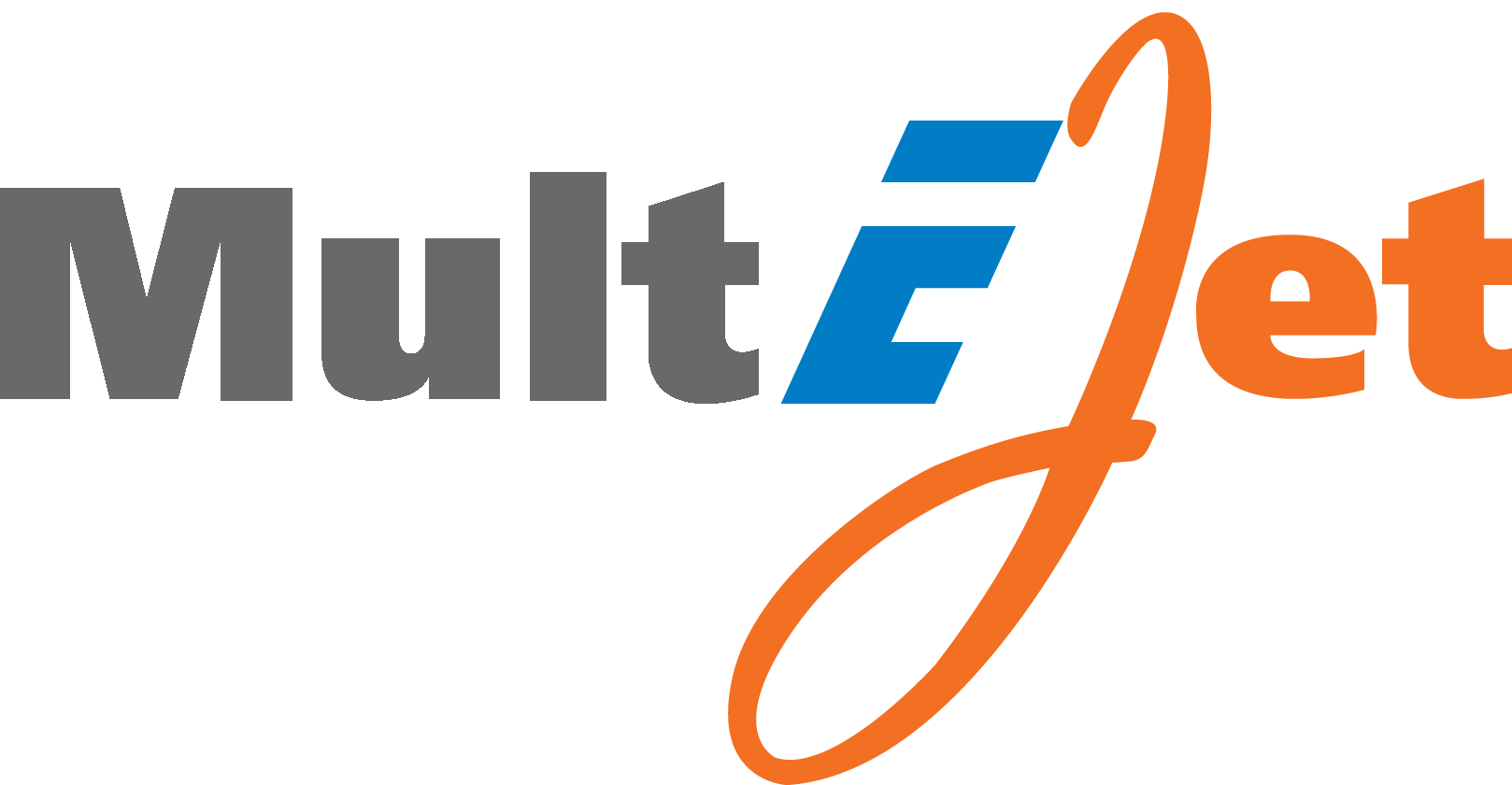
Diesel
Needs to be refueled.
Emits particulate matter, nitrogen oxides, carbon monoxide etc.
Higher power costs due to diesel engine efficiency of less than 50%.
Engine creates noise during operation.
Engine requires regular maintenance and spares.
Electric
No refueling required.
Zero-emission operation.
Lower power costs through electric driveline efficiency of greater than 90%.
Quieter than diesel units during operation.
Motor requires minimal maintenance and spares.
Benefits
Allows greater selection of jetting lances over traditional dump gun technology.
Allows communication between jetting unit and tooling and also rig control rooms.
Optional availability of remote monitoring and fault finding.
The mounting option may be dictated by the hazardous area standards relevant to the operating location.
Skid – the lightest and most economical solution. Skid-mounted pump units can feature comprehensive on-board controls, local operator panel, be linked to existing control infrastructure, or remotely controlled – whatever the application demands. Skids are generally moved using a forklift truck. However, lifting lugs are an option to allow overhead lifting.
Skid with separate environmental/noise enclosure – all the benefits of the skid with the added protection of an enclosure. The enclosure will offer protection from the elements and a range of noise attenuation options.
Crash frame – a good choice offering a lightweight solution for equipment that requires a level of protection during transportation and onsite movements.
Container – providing maximum protection from transportation operations and environmental conditions. Comes with a choice of noise attenuation options. Can include both fork-lift slots, and lifting eyes.