Work Experience
This week we welcomed two students to our company for work experience. Following the obligatory safety induction and factory tour, the students gained practical experience in four main areas – assembly, engineering, purchasing, and marketing. We will let them describe their experience, or an aspect of it in their own words. We will, however, start of by saying how important work experience is – both for the students and Calder.
The students get the opportunity to experience the workplace. They will see the various aspects to a company and gain an understanding of the complexity of producing a product. They may use their experience to determine that office-based roles are right for them, or perhaps they learn that there is great value in working with their hands.
What do we get out of the week? The opportunity to show the workforce, the business leaders, the innovators, or the entrepeneurs of tomorrow how much the engineering and manufacturing sectors add to our economy. Manufacturing adds value – it creates wealth for the country. Demonstrating this to students can only be a good thing.
Barnaby – proving my thoughts
As I already had an interest in engineering, I chose to do work experience at Calder. I was intrigued by the bespoke pressure systems designed and assembled by the company. During my week at Calder, I was inspired by the complex mechanical engineering that goes into their high-pressure systems to make them reliable and long lasting.
Pump Strip-down
We spent some time with Rob from the service team where we took apart a plunger assembly from the inside of a Hammelmann pump. I was amazed by the very specific sizes of all the small components inside the pump which made it work effectively. As part of the task, I looked at 2D engineering drawings of the pump which showed where the parts fit in.
At Home in Engineering
The most enjoyable part of the week for me was shadowing some of the design team to see how they use Computer-Aided Design software to produce accurate models of pump systems. The designs need to comply with the customer’s application and industry standards. We were then given the opportunity to try some of the software ourselves by creating a couple of components and modifying some example components, which I really enjoyed. This gave me an insight into the day-to-day work of the engineers designing the systems.
We also looked at Finite Element Analysis (FEA) in which I took great interest. FEA ensures that each design will be structurally sound in a range of circumstances by converting a model into a mesh and performing a series of calculations on it based on potential real-world stresses a system could endure. This ensures that any vulnerabilities are found and removed before the product is manufactured to ensure a high standard of quality and endurance from the pump system.
Confirming my Belief
The experience I have gained of the CAD system and FEA has confirmed my belief that I would like to work in an engineering design team. This real-world look at mechanical engineering, which has inspired me to research further into engineering as a career option.
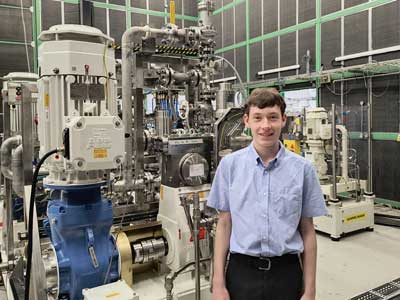
Poppy – thinking again
I came to Calder for my work experience with the rigid mindset that I was only there to get the work experience set by college. Before arriving, my expectations for the week were very limited. I did not think that I would be able to last the week, let alone enjoy it. However, after my time here my view on Calder has changed greatly, through the welcoming staff in particular and the new applicable skills that I have learnt.
A Passion for Computer Science
Through a previous work placement I gained experience with CAD systems, the workshop, and computer software. However, neither the CAD systems nor workshop appealed to me. At the time I did have a passion for computer science but decided it was not something that I could carry out for a living.
Changing Views
I have never been interested in the physical aspect of engineering, but after my week at Calder my views on engineering are not so short sighted. Throughout the week I was posted in different departments, where I got to experience different aspects of the company. In each department I learnt a new skill that can be brought to future jobs and are just generally applicable to life. The skills ranged from physical skills on the shop floor, where I learnt how a pump functions and even got to make my own creation, to the more technical side in the engineering department. I was once again introduced to a CAD system called SOLID EDGE but, despite my initial doubts, I enjoyed using it.
Surprise!
To my surprise, my favourite part at Calder was with Rob, an engineer on the service team. He showed us how a pump is assembled through taking it apart and matching the components to an engineering drawing. The activity was very hands on, meaning I was engaged throughout the task allowing me to enjoy it.
After my time here, my views on engineering as a future career have been reawakened. My work placement at Calder and experiencing what it would be like in an engineering company, has lead me to consider reopening the pathway to engineering.
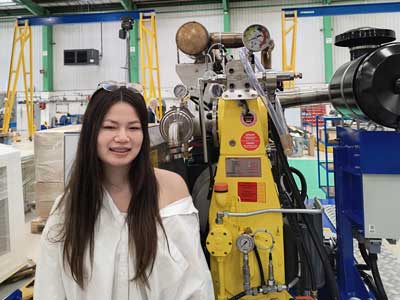
A day with Ray
On the second day we spent time with Ray, one of the engineers in the workshop. We each made a trophy that we could take home. We used scrap parts consisting of a valve from a Hammelmann pump, a high pressure ring, and nuts & bolts – all manufactured in 316L stainless steel. Ray used a lathe to find the centre of the bolt and then made a pilot hole using a drill. He then drilled a hole into it with a diameter of 4.2 mm. After this, we tapped the bolt to create an M5 metric thread. Then we assembled the trophies using a nut and bolt, which we torqued to 94 Newton metres. We then drilled a hole through the high pressure ring and fitted it onto the bolt with an M5 stainless steel bolt. Ray explained the importance of material traceability – in particular where pump systems are used in hazardous areas and for critical applications.
