the challenge
We were approached to design, manufacture and test a high pressure, high temperature (HPHT) pump package for wash down duties on an offshore platform located in the Danish sector of the North Sea. The project required compliance with NORSOK coupled with the client’s stringent process design specifications. A product to meet the high flow and pressures stipulated by the end user was not available as an off-the-shelf design, so we designed a unique package to deliver the necessary performance, maintain compliance with user and international specifications, and be completely self-contained within a space-confined footprint.
The client’s project requirements were typically not applied to equipment of this type. This required bespoke and innovative solutions.
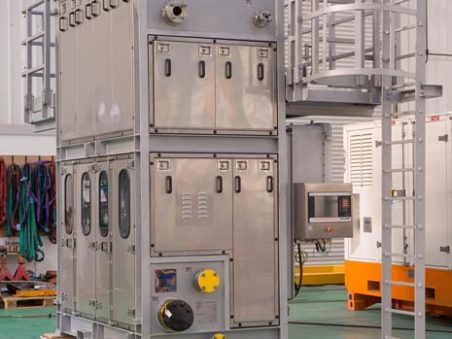
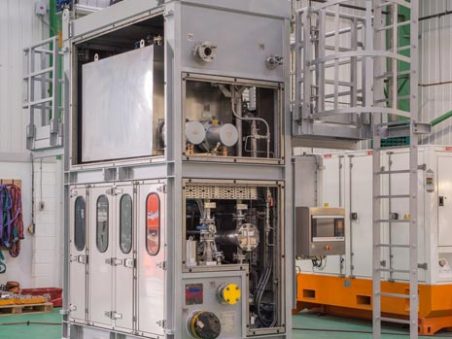
the solution
The main motor variable frequency drive for the wash down pump was required to be located in an ATEX Zone 1 Hazardous Area. A certified device for this hazardous area application is not available, so our engineers worked in conjunction with an ATEX Exd enclosure manufacturer to design and manufacture a solution, and then had it independently certified. The final design was sent to an independent agent to verify the enclosure’s ability to withstand an internal explosion.
With limited on-board deck space and a requirement for water jetting applications at multiple locations on the offshore platform, a solution was required to deliver high pressure water to multiple users from a single pump package. We designed a single pump system capable of delivering the total demand for flow into a ring main that was piped throughout the platform where users could connect locally for water jetting service. We developed and tested both the control system and software to operate the pump at variable flow rates to suit downstream user demands.
High pressure, high temperature, wash down pump packages are typically determined to be utility equipment. The customer’s requirement was for a package that complied with process design specifications and philosophies. We developed a design to integrate high specification water jetting equipment with process type components/materials which included the integration of complex redundancy into the control system.
The area designated for the siting of this pump package was derived during the early Front End Engineering Design (FEED) stage and based on the dimensions of a standard pump package of much smaller capacity. This created a major space constraint, so we designed a unique installation that included a considerably larger capacity pump that spanned two levels to achieve the small design footprint requirement. The development proved challenging due to the requirement to integrate the drive and controls onto the unit in a hazardous area which would normally be located elsewhere in a safe area.
The Pressure Equipment Directive (PED) has to be applied to all pressure equipment being used in Europe as part of CE marking requirements. The PED evaluates the suitability of a piece of pressure equipment to operate safely over its operational life. The high pressure, high temperature wash down pump package needed to be evaluated as a category three unit, which involves the use of an independent, notified body. All pressure systems have to include a safety system, the last line of which will be a pressure safety valve (PSV) which opens and relieves pressure at a set pressure point. The client’s specification requested that the PSV have isolation valves up and downstream of it. In terms of the PED this is not acceptable due to the potential blocking of a safety system; as such the notified body would not approve the package. The client would not relax their specification either. To overcome this, our project and engineering team worked with the client and the notified body to develop a robust system of work which would ensure that the valves were never accidentally operated or left in the wrong position during operation. This involved developing work procedures and modifications to the valves to ensure they could be locked.
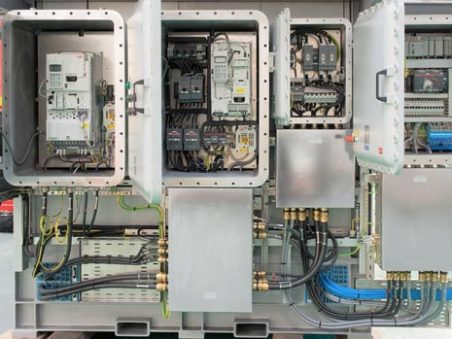
the result
The project was a complete success. The pump package design was proven to be technically compliant through the use of detailed engineering analyses, and then thoroughly tested during the Factory Acceptance Test phase. Successful inspections by third party organisations approved the package as compliant with legislative requirements. The end user now has a robust, high quality wash down system to provide water jetting services at multiple points around the platform – supplied from a single pump source.
Check out our standard and bespoke hot wash units.
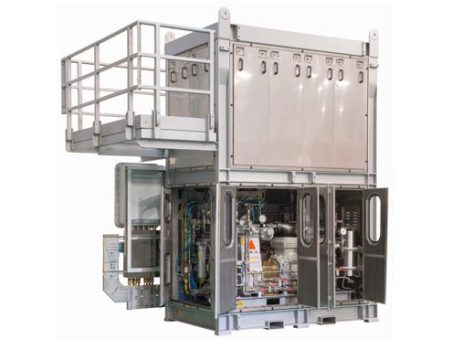
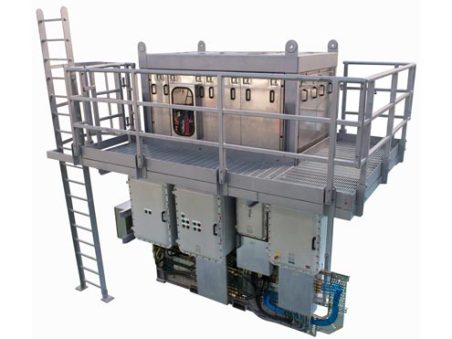
See our Hot Water Jetting product page for more information on our standard and bespoke hazardous area hot water pump units.
To discuss your requirements in detail, please call us on +44 1905 751790 or email sales@calder.co.uk .