The challenge
Standard reciprocating pump lubrication systems generally require pressurized oil to be supplied to the main slideways and contact surfaces within the HP gearbox, crankshaft and crosshead areas to ensure adequate lubrication and low friction operation. The industry standard is to provide a fixed speed external lubrication pump system which pumps oil at a fixed flowrate, regardless of the flowrate actually required by the main process pump. As the oil temperature increases during use, the oil viscosity reduces and, therefore, the process pump requires a higher flowrate of oil. However, the traditional oil pump solution is a single, fixed flowrate oil pump, sized so that it can pump the maximum flowrate of oil which the process pump could ever potentially accept, plus a margin for safety. This means that for much of the time, especially during start-up when the oil is not up to full operating temperature, the oil pump is producing far more flow than can be accepted and used by the main process pump. This excess flow has to be diverted via a ‘spill back’ type ‘bypass’ regulating valve to the oil tank. This additional pipework and spill back valve take up valuable skid space and increase skid weight.
The solution
A recent project required the pump package to fit within an extremely small footprint, but at the same time include a considerable amount of instrumentation equipment. One of the solutions to this challenge was Calder’s development of an innovative pump lubrication system. Unlike a standard ‘fixed flowrate’ lubrication oil system, Calder’s new system delivers the required oil flowrate and pressure at all times, and does not have to return any unused oil back to the tank. This is particularly important when the oil temperature is low, and viscosity is high.
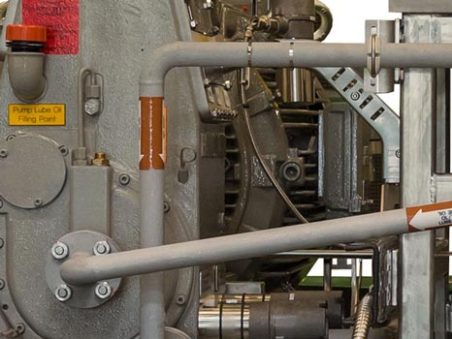
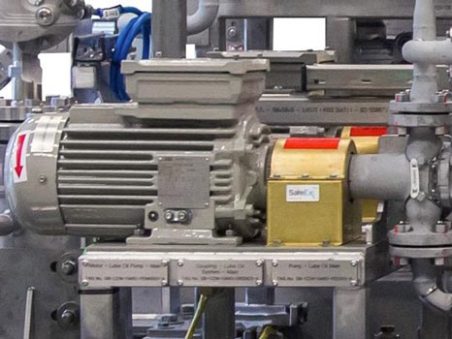
The result
A pump unit with our new pump lubrication system which benefits from:
- space saving through the elimination or downsizing of some mechanical items such as regulating valves, and temperature control valves and their associated pipework.
- a stable system pressure which is maintained (within 0.1 bar) via rapid reaction to pressure changes.
- smooth starting leading to no peak electrical motor current overload current penalties at low temperatures, normally caused by cold high viscosity lube oil.
- less stress on mechanical parts and unlimited start-ups.
- a fixed power factor.
- indirect energy savings which add up to another 10 percent due to lowered net pressure, thereby reducing system pressure and reducing leakages.
- low lube system noise.
Check out our pump products for the energy sector.

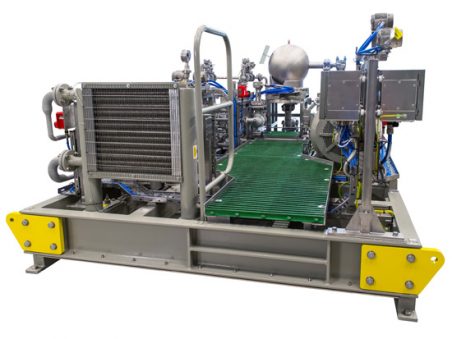

